|
|
|
|
Suitable for hard grinding and grinding of hole and OD gears.
MCR-ST radial and front clamping. The gear is loaded manually or automatically, pre-set through the pre-locators then clamped by the locators. Once the arms have closed down, the rigidity applied allows for hard machining. The mechanism driving the arms can swivel allowing a corrective stirrup effect. When machining the taper gear the carrier is still clamping the work piece.
MCR – Radial clamping. The gear is located on the carrier, pre-set through the pre-locators then clamped by means of locators. The mechanism is driven by one rotary cylinder. The machine can machine the gear hole and the taper. |
|
|
|
|
|
|
|

|
|
Main Features
- High rigidity during machining
- Repeatability accuracy within 0.01mm
- Quick change without any further adjustment
- High centring accuracy on primitive gear pitch circle diameter
- High bore roundness accuracy in bore
- High rotation speed
- High cutting on hard turning
- Suitable to machine outer taper by means of recovering arms
- Manual or automatic loading
- Gear presence check (PEL)
|
|
|
|
|
|
|
|
Automatic carrier for gear hole grinding, modular system for small production lots |
^Top |
|
|
|
|
|
|
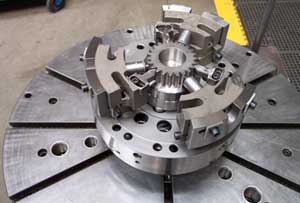 |
|
Basic Features
- Absolute modularity by means of angular adjustment of the bases holding locators and pre-locators in short time
- Very high repeatability accuracy (within 0.005mm)
- Loading both manual or automatic
- Predisposition for work piece check
- Predisposition for coolant passage
Main Features
- High accuracy granting a repeatability lower than 0.005mm
- The use of presetted calibres allowing the clamping of a wide range of gears with different teeth number.
- Quick change
- Modularity for clamping different gears with different OD and teeth number.
|
|
|
|
|
|
|
|
Automatic device for small size taps (M3-M30) driving on a grinding machine on centers |
^Top |
|
|
|
|
|
|
 |
|
Main Features
- Driving by means of clamping without influencing the positioning got by centers.
- Quick set up
- Feeding both pneumatic and hydraulic
- Loading both manual and automatic
- Specific sizing to allow passage of grinding wheels for multi directional machining
- Centrifugal force balancing
- Protections against dirt
|
|
|
|
|
|
|
|
Automatic Chucks for alloy wheels clamping |
|
|
|
|
|
|
|
Automatic axial bracket chuck for 5 arm wheels, mechanic anti-vibrating system |
^Top |
|
|
|
|
|
|
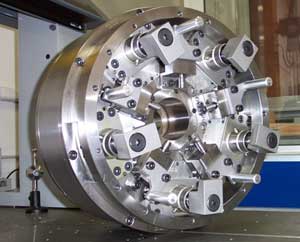 |
|
- Automatic carbon fibre bike wheels clamping chuck
- Automatic chuck for alloy wheels clamping centring by means of 3 radial jaws, clamping by means of 3 axial arms
- Automatic long jaw stroke for soft clamping and centrifugal force and compensation
- No distortion automatic radial clamping chuck, centrifugal force compensation.
- Automatic axial bracket chuck for 3-5 arm wheels, mechanic anti-vibrating system
|
|
|
|
|
|
|
|
Transfer Machines |
^Top |
|
|
|
|
|
|
 |
|
- Two jaws with high precision repeatability self centring device, accuracy less than 0.005mm. Hydraulic built in cylinder, high rotation speed, low impact of centrifugal force on the system, with internal passages for air pressurizing
- Two long stroke jaws compact self-centring device
- Two jaws self- centring device, high precision, repeatability, high clamping force. Built in cylinder
- Device with independent axial and rotating stirrups
- Long stroke compact self centring device, technical features similar to point 2 above but water-proof.
- Compact device with 1 fix and 1 moving jaw, with built-in hydraulic cylinder, palletized with jaw quick change
|
|
|
|
|
|
|
|
Special centring and stirruping clamping system for NC turning- grinding- milling machine for
automatic loading |
^Top |
|
|
|
|
|
|
 |
|
The system is complete with two independent mechanisms. The first one is moving the central expander having stroke mm 7 on diameter, centring the work piece from the inside. The second one is linked to a moving plate driving 3 rotating and stirruping shafts. These are clamping the work piece granting stiffness during machining. Both systems are driven by a double cylinder. There is a PEL detection system checking the right positioning of the work piece by the robot. The change of work piece type is very fast thanks to quick coupling systems of different components. |
|
|
|
|
|
|
|
|
|
|
|